|
|
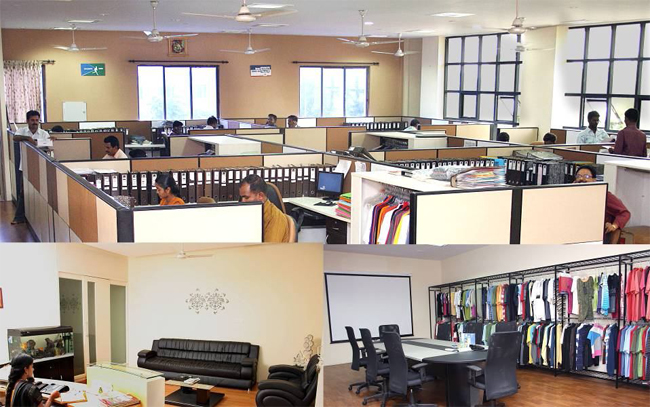 |
|
|
The growth of RBR can be
attributed to keep the commitment
towards high standards of quality, both
in the production process and the end
products. Undoubtedly the management
and the employee are a well-knit team
dedicated to deliver quality. The result
of devoted hard work and acumen in
selecting the right person to the right job
has capitulated good results. |
|
|
|
|
OUR INFRASTRUCTURE & FACILITIES |
|
|
|
|
|
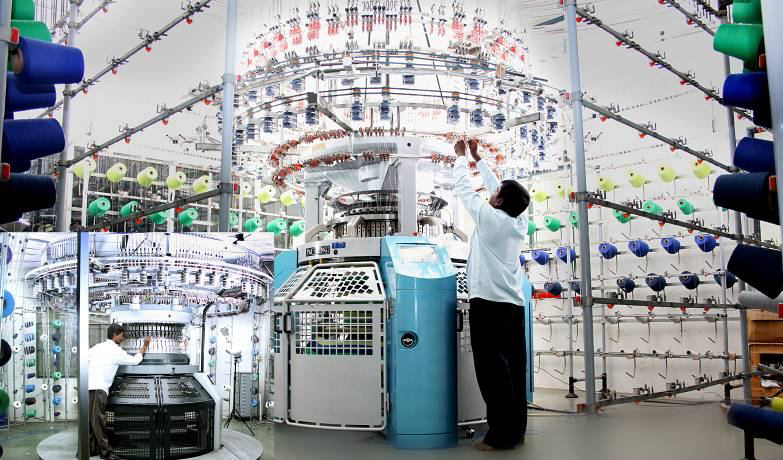 |
|
|
The Very latest 16,20,24 & 28 Gauge Circular Knitting machine are engaged in the production floor like “ Mayer & Cie” from Germany, Italian
“ Orizio Paulo” A variety of knitted fabrics are produced starting from the basic jersey, Interlock, Pique, Rib, Auto striper With 70 Color + Lycra,
Jacquard + Wrapper with 72 color + Lycra.
Collar : - 16 & 114 – Plain + Platted jacquard.
|
|
|
|
|
|
|
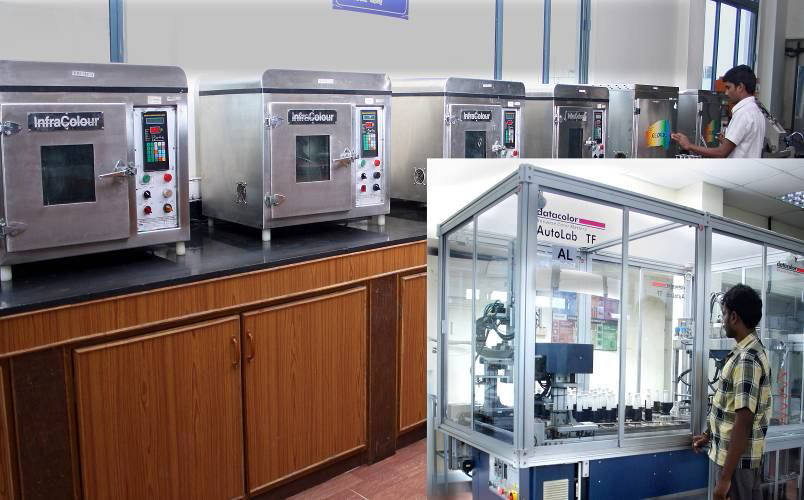 |
|
|
Fully automated Lab
dispenser / Colour matching
SPECTRO-SF 600 and I.R
Lab dyeing machines helps
100% accuracy |
|
|
|
|
|
|
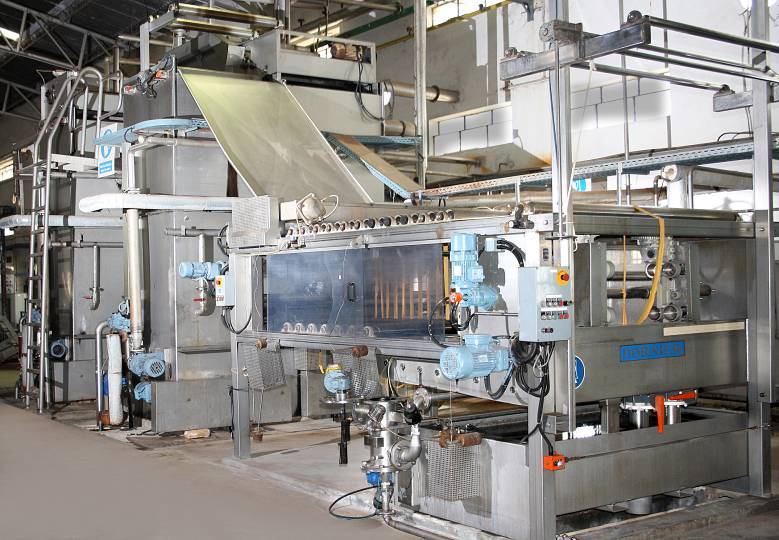 |
|
|
The RBR fabrics undergo value
addition by its additional special
Mercerizing process. The mercerizing
is done by the only world’s best
“Dornier” Germany Mercerizing
machine. The specialty with our latest
machine is also due to its circular
expandable four tower washing
facility which is also fully automated,
yielding high luster, and intense color
depth leaving a very good hand feel. |
|
|
|
|
|
|
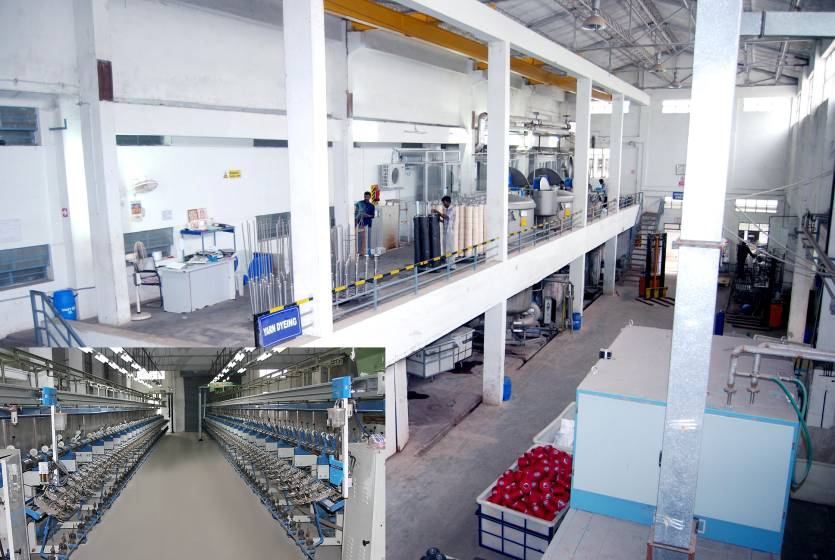 |
|
|
“Dilmenler” yarn dyeing
machines are used for an
uniform, best and
reproducible shades. This is
supported further by
Mesdan-Italy wet splicing
for a smooth knotless knitted
stripes and check. |
|
|
|
|
|
|
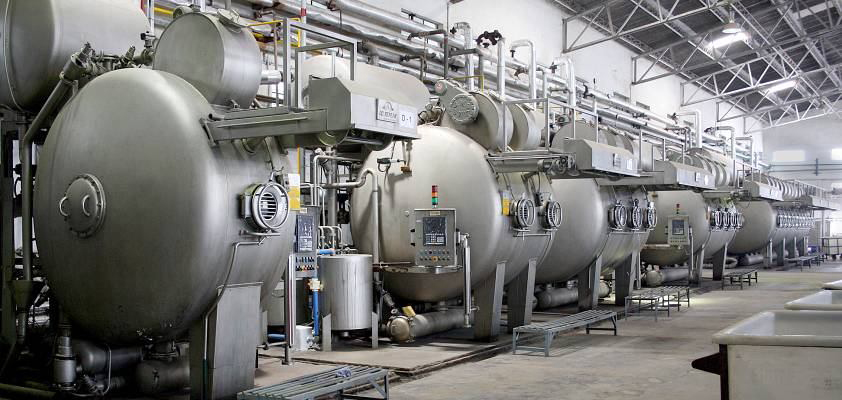 |
|
|
“Dilmenler” Modern HTHP
Soft Flow Dyeing
Machines with superior
control parameters latest
SETEX 838 PLC
Controller |
|
|
|
|
|
|
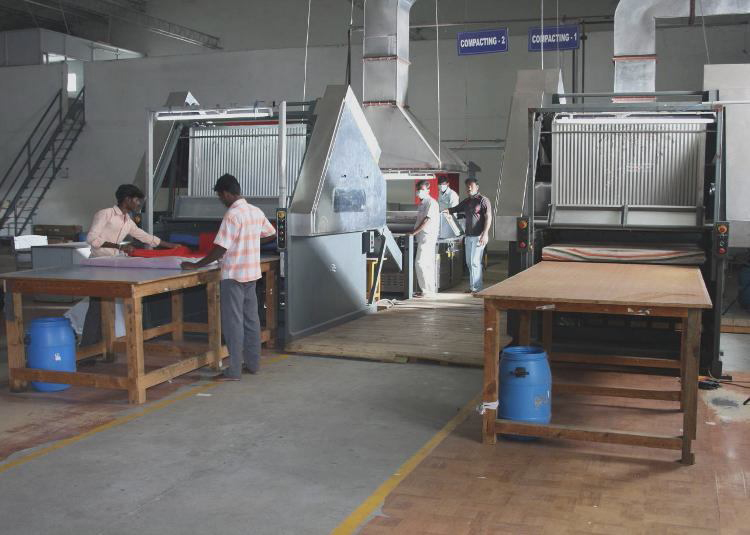 |
|
|
The washed and laundered
cloth is sent through the
latest “Tube-tex” USA
compacting machine to
control shrinkage. All
processed fabric is preshrunk,
so that the
garments always retain
shaped. |
|
|
|
|
Finishing Touch
|
|
|
|
|
|
|
|
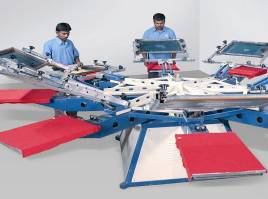 |
|
According to the requirements of printing, the
Cloth is processed for various colors and
other specifications. Fully automated multicolor
printing is done to satisfy all quality
requirements. |
|
|
|
|
|
|
|
|
|
|
|
|
This department has the world’s best Japanese
“Barudan” automatic high-speed embroidery
Machines, they are capable of rendering multi
colors of embroidery and appliqué, an art
which enhance the value of the garments.
Capacity 1.5 Billion Stitches per day. |
|
|
|
|
|
|
|
|
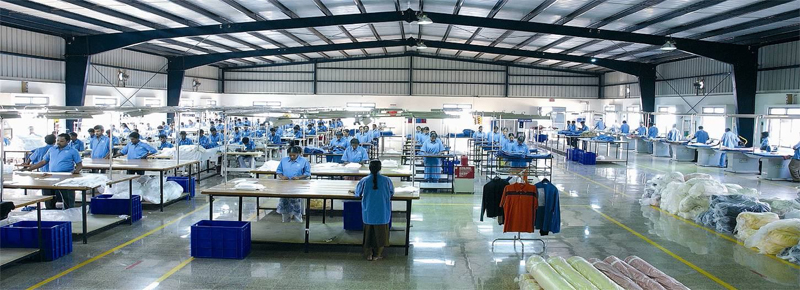 |
RBR has in its production line the best and truly sophisticated machinery capable of
producing productivity and quality. To minimize the wastage in fabric, the planning of cut
layout is done with the help of CAD “Investronica” to utilize resources of men & machine
more efficiently, the production monitoring is done with barcode systems. |
|
|
|
|
|
|
|
|
|
|
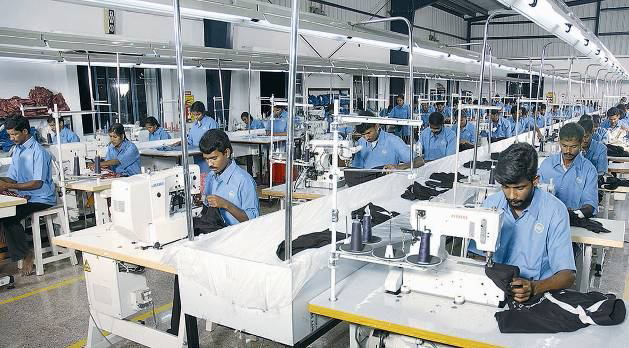 |
|
The Production line for finishing has high-tech
1500 machines like PEGASYS, JUKI, SIRUBA
and BROTHER. The well trained and skilled
workforce engaged in 34 Lines around 34,000
pcs per day basics men’s polo stitching are
supported by highly experienced line supervisors
and Quality Controllers, who check on every
garment under production to ensure flawless
stitching. And finishing all garments is steamironed
and machine pressed meticulously. All the
garments are hand packed with care and stored
for subsequent transportation to various
destinations. |
|
|
|
|
|
|
|
|
|
|
|
|
|
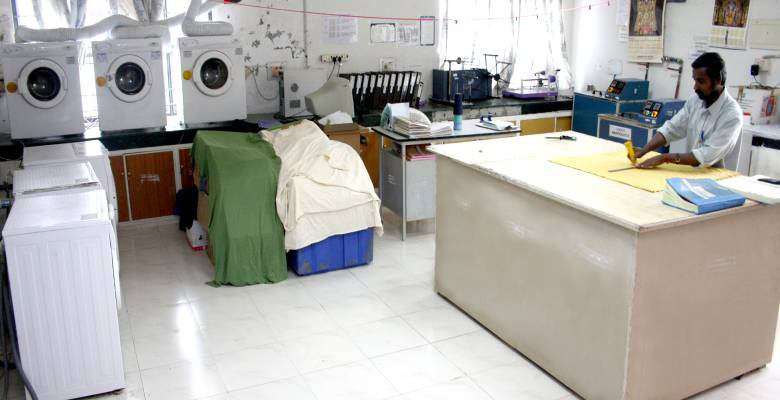 |
|
Various Parameters are constantly
checked, monitored and controlled in
the production process. All
recommended tests are conducted for
ascertaining Quality standards
specified by various statutory agencies
of the relevant countries, as per buyers
requirements. Critical focus is kept on
Cotton, Yarn and knitted cloth Quality. |
|
|
|
|
|
|
|
|
|
|
|
|
|
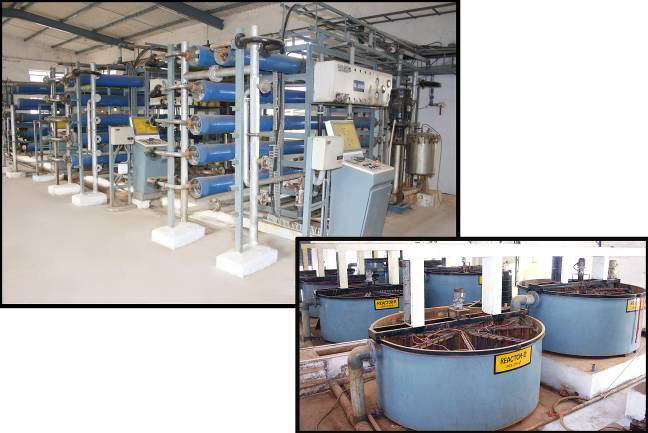 |
|
Understanding the need to
preserve the precious resources
of the Mother Nature, RBR has
taken particular care in making
its production process and
resources, eco-friendly. A
“Reverse osmosis” plant with
multiple Evaporators ensures
effluent treatment of 0%
discharge. |
|
|
|
|
|
|
|
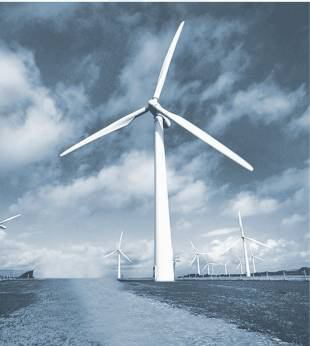 |
|
|
|
|
|
The need to generate “Green Power” Motivated RBR to set up
its own wind mills to produce electric power for internal |
|
|
|
|
|
|
|
|
|